Tech
Common Wire Splices and Joints (Detailed Guide)

Having the skill to splice and join wires is essential whether you are a seasoned electrician or a novice DIYer. This comprehensive guide, crafted by experts, will unravel the mystique around common wire splices and joints, equipping you with the knowledge to tackle your electrical projects confidently.
Table of Contents
Understanding Electrical Wire Splices and Joints

The art of connecting electrical wires, also known as splicing, is a fundamental skill in electrical work. Wire splices and joints facilitate the smooth transmission of electrical current from one wire to another. This process may sound simple, but the quality of the connection can significantly impact the performance and safety of your electrical system.
The Anatomy of a Reliable Wire Splice
Splicing techniques can vary, but they all revolve around ensuring that the integrity of the electrical connection is not compromised. There are three core attributes to a reliable wire splice:
- Conductivity: The splice must allow the electrical current to flow seamlessly from one wire to another.
- Insulation: After splicing, the joint should be properly insulated to prevent short-circuits or shocks.
- Stability: A good splice should be strong and stable, even when subjected to tension or twisting forces.
Unleashing the Power of Different Wire Splices and Joints
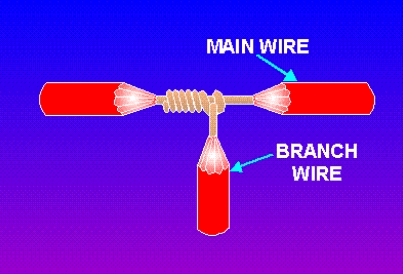
There are several methods of connecting wires, each with its unique strengths. Understanding these types will enable you to choose the best approach for your project. Here are the most common types of wire splices and joints:
Twist-On Wire Connectors
Often referred to as wire nuts, twist-on connectors are incredibly popular due to their ease of use. They are perfect for joining two or more wires without soldering. However, their application might be limited outdoors as they are not inherently waterproof.
Soldered Wire Connections
When a secure and long-lasting splice is needed, soldering is the go-to technique. Despite requiring more skill and equipment, soldered connections are highly reliable and ideal for many applications, including those demanding high current flow.
Crimp Connectors for Wire Splicing
Crimping provides a mechanical method for joining wires. It’s efficient and doesn’t require heat, making it suitable for various environments. A crimped connection is only as good as the tools and technique used, so proper crimping practice is paramount.
Butt Splice Connectors
These are ideal for connecting wires end-to-end, especially in tight spaces. Butt splice connectors come in insulated and non-insulated versions, and using heat shrink tubing can add an extra layer of insulation and stability.
Heat Shrink Wire Splices
These special connectors come with a heat-activated adhesive lining. When heat is applied, they shrink to form a tight, waterproof seal around the splice. They are ideal for outdoor applications or where exposure to moisture is a concern.
The Exciting World of Wire Splicing Techniques
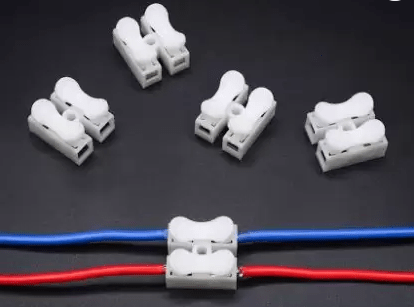
The Western Union Splice
The gold standard in wire splicing, especially when soldering is involved. It offers a strong mechanical bond and excellent conductivity, making it perfect for many applications.
The Tap Splice
Used when a wire needs to be connected to a running wire without cutting it. This splice can be used in cramped spaces and is ideal for temporary connections.
The Fixture Splice
Also known as a pigtail splice, it is commonly used to connect a fixture like a switch or an outlet to a circuit. It’s simple to perform and extremely practical in household wiring.
Rat-Tail Splice
Ideal for connecting two or more solid wires, this splice is popular due to its simplicity and efficiency. It requires a twist-on connector or electrical tape to insulate and secure the splice.
Safety Measures and Best Practices in Wire Splicing
Safety should never be compromised when dealing with electrical connections. Here are some safety precautions to consider:
- Always ensure the power is off before beginning any electrical work.
- Use tools designed for electrical work, such as wire strippers and lineman’s pliers.
- Insulate all splices properly with wire nuts, electrical tape, or heat shrink tubing.
- Test every connection for stability and continuity before restoring power.
- Follow local electrical codes and standards for wire splices and joints.
Wire Splicing Troubleshooting and Common Mistakes to Avoid
Poor Conductivity
The main purpose of a splice is to facilitate the smooth flow of electricity. A poorly made splice can restrict this flow, causing heat buildup, reduced performance, and, in extreme cases, fire hazards. To avoid this, ensure that all wire strands are securely connected, and there’s sufficient metal-to-metal contact.
Inadequate Insulation
Leaving a splice uninsulated is an invitation to electrical faults and potential shocks. Always insulate your splices, either with suitable wire connectors, electrical tape, or heat shrink tubing. It’s also vital to ensure the insulation covers the entire exposed metal part of the splice.
Loose Connections
A splice that comes apart easily isn’t just an inconvenience—it’s a potential danger. When creating your splice, ensure it can withstand tension without slipping. In crimping, use the correct tools and technique to achieve a secure and tight connection.
The Intricacies of Splicing Different Wire Gauges
Occasionally, you may need to splice wires of different gauges together. This situation requires extra caution because the wire connectors you typically use might not secure the thinner wire properly. Specialized connectors designed to handle different wire gauges, such as step-down butt connectors, can be used in such cases.
Working with Aluminum Wires
Aluminum wires require special considerations due to their unique properties. They are softer and can easily break during splicing, and they also have a different coefficient of expansion compared to copper. Use only connectors marked AL/CU or CO/ALR, specifically designed for aluminum to copper connections.
The Delicate Dance of Wire Splicing in Tight Spaces
Splicing in confined spaces or corners can be tricky due to limited maneuverability. In such situations, fixture splices or tap splices may be advantageous. These techniques require less space compared to others like the Western Union splice.
Alternatives to Wire Nuts
While wire nuts are a common choice for many splicing applications, there are alternatives available for different scenarios. Push-in connectors are a fast and easy alternative, especially for solid wires. For a more secure and waterproof connection, you can use heat shrink wire splices.
The Role of Electrical Tape in Wire Splicing
The use of electrical tape in wire splicing isn’t necessarily a must but can be an added measure of security and insulation. In some cases, like with a rat-tail splice, it might be the primary method of insulating the splice. However, it’s generally recommended to use other more secure methods of insulation, such as heat shrink tubing or wire connectors, where possible.
Industry Standards and Codes for Wire Splices and Joints
Following industry standards and codes isn’t just about compliance—it’s about safety. The National Electrical Code (NEC) in the US sets guidelines for splicing and joining wires, which vary depending on wire type, location, and application. Always familiarize yourself with these codes and guidelines to ensure your work is safe and compliant.
Understanding the Difference Between a Splice and a Junction
While these terms are sometimes used interchangeably, they represent different concepts in electrical work. A splice refers to the actual connection where two or more wires meet and are joined. A junction, on the other hand, is a box or enclosure where splices are often housed for protection and ease of maintenance.
Also Read: The 3 Key Components of a CNC Lathe Machine
Closing Thoughts
Mastering wire splicing and jointing techniques can be a game-changer for your electrical projects. However, always remember that knowledge without proper safety practices is a recipe for disaster. Treat electricity with respect, always adhere to the rules, and don’t hesitate to seek professional help when necessary.
We hope this comprehensive guide about “Common Wire Splices and Joints” provides you with a clearer understanding and appreciation of wire splices and joints. Armed with this knowledge, you can confidently tackle your electrical projects while prioritizing safety and efficiency.
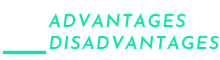
-
Health5 years ago
Advantages and Disadvantages of Milk
-
Tech4 years ago
6 Tips to Improving E-Commerce Websites
-
Home5 years ago
Advantages and Disadvantages of Village Life in Points
-
Travel5 years ago
Advantages and Disadvantage of Travelling
-
Sports3 years ago
The benefits of playing an online live casino
-
Tech5 years ago
10+ Advantages and Disadvantages of Mobile Phones in Points
-
Tech5 years ago
Essay on Advantages and Disadvantages of Offline Shopping
-
Tech5 years ago
8+ Advantages and Disadvantages of Motorcycle |Having Bike