Education
How are customized magnets made?
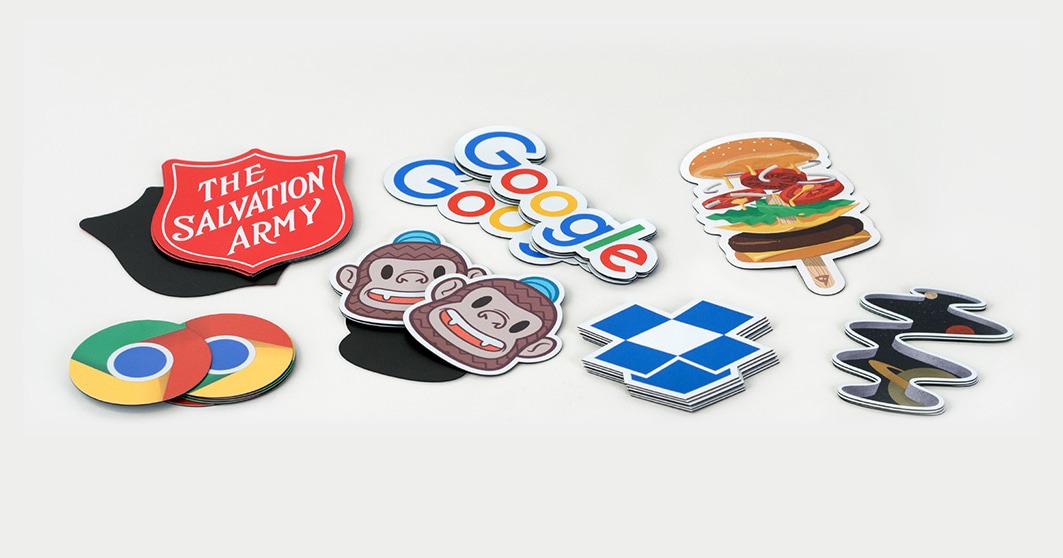
Magnets have long held a fascination for us. From their use in everyday items like refrigerator magnets to complex scientific applications, magnets play a crucial role in our lives. But have you ever wondered how customized magnets are made? In this article, we’ll delve into the fascinating process behind the creation of customized magnets, shedding light on the intricate techniques and materials involved. So, let’s embark on a magnetic journey!
Table of Contents
The Basics of Magnets
Before we dive into the manufacturing process of customized magnets, let’s understand the basics. Magnets are objects that produce a magnetic field, which attracts certain metals like iron, nickel, and cobalt. This magnetic field is created by aligning the atomic particles within the magnet in a specific manner. Magnets have two poles, known as the north and south poles, which exert attractive or repulsive forces on other magnets or magnetic materials.
How Customized Magnets Are Made?
Now that we have a basic understanding of magnets, let’s explore the intriguing process of creating customized magnets. The manufacturing process involves several steps, combining scientific principles, engineering expertise, and advanced technologies. Here’s a breakdown of the process:
Step 1: Material Selection
The first step in creating customized magnets is selecting the appropriate materials. Magnets can be made from various materials, including ferrite, neodymium, and samarium cobalt. The choice of material depends on the desired magnetic properties, such as strength, temperature resistance, and cost-effectiveness. Each material has its unique characteristics, making it suitable for specific applications.
Step 2: Formulation and Mixing
Once the material is selected, it undergoes a formulation and mixing process. In this step, the raw materials are combined in precise proportions, taking into account the desired magnetic properties. The mixing process ensures a homogeneous distribution of the materials, resulting in a consistent magnet composition.
Step 3: Shaping and Molding
After the mixing process, the magnet material is shaped into the desired form. This can be achieved through various methods, such as compression molding, injection molding, or extrusion. Compression molding involves applying pressure to the material to create a solid shape, while injection molding uses a heated mold to inject the material into a cavity. Extrusion, on the other hand, involves pushing the material through a die to obtain the desired shape.
Step 4: Sintering
Sintering is a critical step in the manufacturing process of magnets. It involves subjecting the shaped magnet material to high temperatures, typically in a controlled atmosphere. During sintering, the material particles fuse together, forming a solid structure. This process enhances the magnetic properties of the magnet and ensures its structural integrity.
Step 5: Machining and Finishing
Once the magnet is sintered, it undergoes machining and finishing processes to achieve the desired shape and dimensions. Precision machining techniques, such as grinding, cutting, and drilling, are employed to create intricate designs and precise tolerances. After machining, the magnets may undergo surface treatments, such as coating or plating, to enhance their durability and resistance to corrosion.
Step 6: Magnetization
The final step in the manufacturing process is magnetization. This is where the magnet is exposed to a strong magnetic field to align its atomic particles and establish its north and south poles. Magnetization can be achieved through various methods, including passing the magnet through a coil or using a pulse magnetizer. Once magnetized, the customized magnet is ready to fulfill its intended purpose.
Conclusion:
In conclusion, the process of how customized magnets are made involves a blend of science, engineering, and craftsmanship. From material selection and mixing to shaping, sintering, and magnetization, each step contributes to the creation of magnets with unique properties and applications. Customized magnets play a vital role in various industries, offering versatile solutions for diverse needs. So, the next time you hold a magnet in your hand, remember the fascinating journey it took to come into existence.
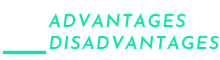
-
Health5 years ago
Advantages and Disadvantages of Milk
-
Tech4 years ago
6 Tips to Improving E-Commerce Websites
-
Home5 years ago
Advantages and Disadvantages of Village Life in Points
-
Travel5 years ago
Advantages and Disadvantage of Travelling
-
Sports3 years ago
The benefits of playing an online live casino
-
Tech5 years ago
10+ Advantages and Disadvantages of Mobile Phones in Points
-
Tech5 years ago
Essay on Advantages and Disadvantages of Offline Shopping
-
Tech5 years ago
8+ Advantages and Disadvantages of Motorcycle |Having Bike